Новости
Недавно на территории Барнаульского завода механических прессов появилась новая вывеска: «Завод тяжелых колесных дисков».
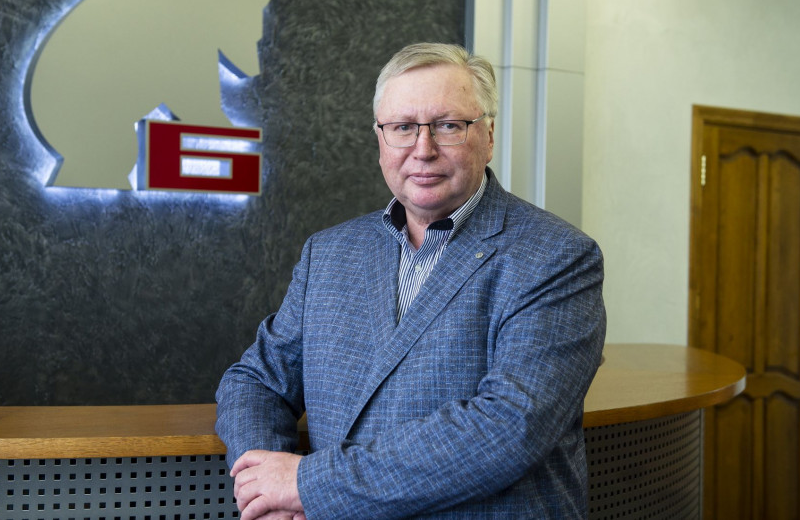
Здесь уже производятся диски для крупной сельхозтехники: тракторов, комбайнов, опрыскивателей. Предприятие отгружает продукцию Петербургскому тракторному заводу, на «Ростсельмаш» и «Гомсельмаш». Но это только начало, поскольку тракторами и комбайнами номенклатура не ограничивается. Тем более, что аналогов в России нет. О том, как создавалось это уникальное для страны предприятие, мы
Факт Размер выпускаемых заводом дисков может доходить до 54 дюймов, а вес — достигать 200 килограммов. Сергей Ферапонтов.
Фото: Анна Зайкова.
|
— Перед тем, как перейти к разговору о новом производстве, хочу
— Этот год был годом развития, мы приросли в объемах производства более чем на четверть.
Впервые за много лет предприятие смогло сформировать полный портфель заказов по производству механических прессов на 2024 год. Сейчас принимаем заказы на 2025-й.
Но, конечно, главный итог — запуск завода тяжелых колесных дисков. Нам удалось снять вопросы по всем технологическим переделам, запустить автоматизированные линии, выйти на все нужные параметры производства. Это позволяет надеяться, что в наступившем году мы сможем, как и было предусмотрено бизнес-планом, выйти на проектную мощность.
— Последним звеном в создании этого предприятия, насколько я понимаю, стала линия катафореза. Сегодня мы ее смогли посмотреть в деле. Честно скажу — впечатляет. Происходит сложный химический процесс, этапы которого контролирует специально созданная лаборатория. Выходит, машиностроители стали химиками?
— Отчасти да. Но без наших традиционных компетенций вряд ли бы мы
Фото: Анна Зайкова
Над проектом работал большой коллектив инженеров. Спроектировали специальную котельную для подогрева ванн, компрессорную станцию, узел подготовки воды — она в процессе нужна практически дистиллированная.
Задач хватило и энергетикам, и механикам, и строителям. Сами, к примеру, научились заливать промышленные полы. А некоторые наши специалисты действительно были вынуждены подробнее
— Заметил, что новое производство оснащено вашими же механическими прессами. И механизация вокруг них для перемещения громоздкой тяжелой продукции тоже собственная.
— Это так. Поскольку вес некоторых изделий доходит до 200 килограммов, перемещения от станка до станка важно было максимально облегчить. А прессы в техпроцессе задействованы наши, потому что они были спроектированы и сделаны нами для этого производства. В том числе и первый, созданный нами в прошлом году не механический, а гидравлический пресс.
Сначала решили испытать его на собственном производстве, чтобы можно было показывать его нашим клиентам в деле. Сейчас он встроен в линию по изготовлению ребер и производит запрессовку ребра в обод.
На текущий момент мы подготовили инструмент и ведем работу по изготовлению ребра в 42 дюйма для опрыскивателей, которые изготавливаются в Самаре.
Фото: Анна Зайкова
— Что еще вам пришлось сделать собственными силами?
— Полностью спроектировали и изготовили линию по производству ребер колесных дисков. На этой линии тоже возникало немало интересных технических задач.
Так, вес штампа для подобного производства достигает трех-пяти тонн. Представляете, насколько сложно его менять, переходя на другой диаметр. Наши специалисты предложили сделать блок штампов всех производимых диаметров — один на все, в котором нужно только сменить пуансон и матрицу. Это реально экономит и время, и силы.
Фото: Анна Зайкова.
Испытательные стенды радиальной и осевой нагрузки, через которые должен пройти каждый диск, спроектировали и сделали сами. Доработали линию продольно-поперечной резки рулонной стали, автоматизировали резку и укладку заготовок. Создали механизированный удобный склад готовой продукции…
Общая площадь, которую занимает завод, составляет 16 тыс. кв. м. И нет такого места, над которым бы не поработали наши специалисты. Считаю, что запуск завода — это большая заслуга нашего уникального коллектива, где расчет и инженерная мысль зачастую
— Не слишком ли узок сегмент рынка, который вы закрываете?
— Отнюдь. Вслед за сельхозмашиностроителями начали вести
Подсмотрели у крестьян еще один вид продукции, так называемую спарку, которая позволяет поставить на трактор не четыре колеса, а сразу восемь, по два на каждую сторону оси. Это позволяет в некоторых регионах страны на две недели раньше начать посевную. Производство таких спарок мы наладили и сегодня поставляем их на вторичный рынок.
— Сколько средств было вложено в проект, и как вы их нашли? Как видите окупаемость?
— Региональный Фонд развития промышленности выделил нам 200 млн рублей. Большую часть оборудования купили по лизингу. Общая стоимость проекта – около миллиарда рублей. В этом году хотим отгрузить продукции на полмиллиарда. При выходе на полную проектную мощность завод будет производить дисков на сумму более 2 млрд рублей в год.
— Что дальше?
— Продолжим реконструкцию и переоснащение всего предприятия. Возможно, начнем обновлять фасад и заводские стены. Но главный приоритет на 2024 и ближайшие годы — кадры. Будем продолжать повышать социальные гарантии и заработную плату. Потому что без энтузиазма, творческого порыва и желания людей мы вперед не продвинемся.
Как работает линия катафореза Линия занимает 2000 кв. м. Здесь 17 шестиметровых ванн. Плюс две водяных башни. Диски по ваннам парой перемещаются на автоматическом подвесном конвейере. Их отмывают, помещают в специальные растворы, а после они попадают в электролитный раствор, После этого диски перемещают по конвейеру для полимеризации в высокий термотоннель. Далее они едут в покрасочную камеру, где установлены роботы. Потом снова перемещаются в тоннель для сушки. |
Беседу вел Юрий Пургин.